Tandis que l'utilisation des pistons en aluminium est généralisée au sein de l'automobile, les constructeurs montrent un regain d'intérêt pour l'acier, qui permet, grâce ses propriétés mécaniques, de réduire sensiblement la consommation de carburant, un atout de taille pour respecter les normes d'émissions Euro 6.
Avantages et inconvénients de l'acier
L'aluminium présente un avantage, et non des moindres, par rapport à l'acier: sa légèreté. A volume égal, l'acier pèse trois fois plus lourd. Or, le piston est une pièce mobile à haute vitesse et la masse influe sur le rendement du moteur.
Toutefois, l'acier étant beaucoup plus résistant aux vibrations et à la fatigue, la hauteur et l'épaisseur des pistons peut être réduite, ce qui permet de limiter (voire d'éviter) un embonpoint du piston.
La plus faible hauteur du piston réduit la surface de frottement entre le cylindre et le piston, ce qui réduit potentiellement les frottements. D'autre part, ce gain en hauteur permet, au choix, de réduire la hauteur du moteur (installation plus simple dans un environnement compact, meilleure protection des piétons en cas de choc) ou d'allonger la bielle (moins de contraintes latérales entre le piston et le cylindre).
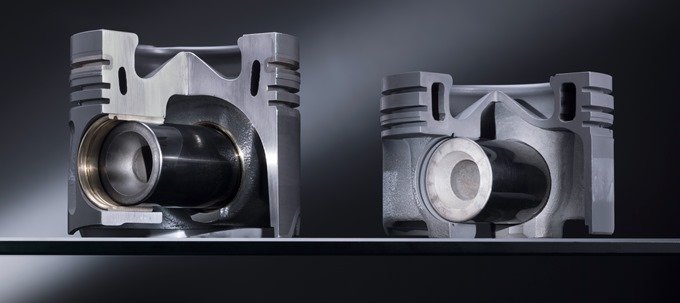
Autre qualité de l'acier: il se déforme moins sous l'effet de la température. Alors que les blocs moteur sont généralement réalisés en fonte (dilatation thermique comparable à l'acier), l'aluminium se dilate beaucoup plus sous l'effet d'une élévation soudaine de température: potentiellement, le diamètre du piston en aluminium peut devenir légèrement plus grand que le diamètre du cylindre dans lequel il coulisse, ce qui génère alors beaucoup de frictions.
Enfin, l'acier est un moins bon conducteur thermique que l'aluminium, ce qui signifie dans le cas d'un piston qu'il y a moins de chaleur dissipée à travers ce dernier et donc, la température de la chambre de combustion est plus élevée. Ce phénomène favorise donc une meilleure combustion (celle-ci étant plus rapide du fait de la température plus élevée) ainsi qu'une réduction des émissions de gaz polluants.
Les pistons en acier sont déjà couramment utilisés pour les moteurs de camions, là où la fiabilité est primordiale et où l'argument du poids est considéré comme secondaire.
Quatres cylindres diesel Renault R9M / Mercedes OM626
Le 1.6l dCi (R9M) est fabriqué au sein de l'usine de Cléon (Seine-Maritime) et développe une puissance de 130 chevaux. Ce moteur est bâti autour d'un bloc en fonte. De fait, le jeu entre le piston et le cylindre (grâce à la dilatation thermique similaire des deux matériaux) reste relativement constant quelles que soient les conditions de température du cylindre, ce qui se traduit par une réduction du bruit et des vibrations lors d'un démarrage à froid et des frictions réduites à tous les régimes de fonctionnement.
L'axe de piston reçoit de plus un revêtement DLC (Diamond Like Carbon - technologie déjà utilisé par la marque pour les poussoirs de soupapes du 1.5l dCi Energy) pour réduire encore les frictions. Le piston reçoit un traitement anti-corrosion. Le gain en matière de consommation est estimé à environ 2%.
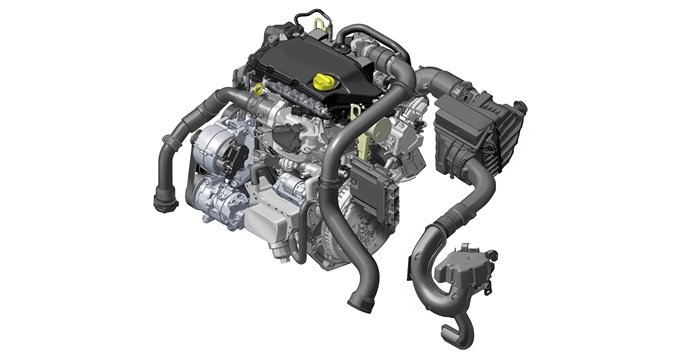
Dans le cadre des accords de coopération signés entre l'Alliance Renault/Nissan et Daimler, Mercedes réalise l'assemblage final (montages d'accessoires spécifiques) des moteurs 1.6l dCi Renault (R9M) dans son usine de Brême (Allemagne). Notamment, les moteurs utilisés par Mercedes sont équipés d'un calculateur, d'un volant moteur, d'un compresseur de climatisation ainsi que d'un démarreur différents de ceux utilisés par Renault.
Le 1.6l dCi Twin Turbo de 160 ch n'utilisera pas à court terme ces nouveaux pistons en acier. Ce moteur a été développé en parrallèle et n'a donc pas pu bénéficier de cette dernière évolution.
Six cylindres diesel Mercedes OM642
Le moteur équipant la Classe E350 Bluetec sera lui aussi équipé de pistons en acier. Contrairement au moteur 4 cylindres Renault, le bloc moteur est constitué d'aluminium. Cette association est problématique, en théorie, du fait des coefficients de dilatation thermique très différents entre les deux matériaux.
Les ingénieurs de Mercedes ont pris le parti de développer un piston dont le jeu est très réduit (assemblage serré) à température ambiante (rendant l'assemblage du moteur plus complexe en usine). De cette manière, dès que le moteur monte en température, le jeu entre le piston et le cylindre devient plus important et réduit sensiblement les frictions mécanique (de l'ordre de 40%).
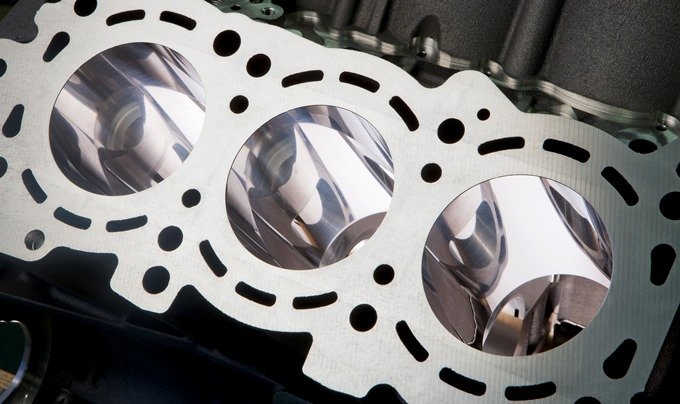
D'autre part, les cylindres ont un revêtement spécial pour réduire encore les frictions. Développé par Mercedes et utilisé uniquement dans les moteurs AMG depuis 2006 (et depuis 2011 dans les 6 cylindres diesel BlueTEC), le revêtement Nanoslide a une épaisseur d'un dixième de millimètre et donne au cylindre l'apparence d'un miroir. Le revêtement est déposé sur le cylindre par projection à l'arc électrique sous gaz inerte.
Grâce à ces mesures, le V6 BlueTEC conserve sa puissance de 190 kW (258 chevaux) tout en abaissant les rejets de CO2 de l'ordre de 3% sur le cycle d'homologation (de 144 g/km à moins de 140 g/km).
Source: Daimler, Mahle, Federal Mogul, KS Kolbenschmidt
Partagez cet article sur :
03 juin 2016 à 20h44
donc ,c'est fini les chemises de cylindres , les cylindres sont directement taillés dans le bloc moteur ! est-il possible d'avoir cylindres et pistons acier à la fois comme sur moteurs de compétition rally ? après les huiles moteurs 100 pour cent synthétiques ont une importance primordiales pour ces nouveaux moteurs et aussi la conduite à froid les 5 à 10 premiers kilomètres ,j'ai déjà entendu parler d'une R5 1200 Cléon faire 50 000 km sans vidange et sans casse moteur ,les constructeurs prennent de la marge pour les conducteurs négligents !